Choosing custom drawer slides can meet your specific space requirements and design needs. Custom drawer slides ensure that drawers are smoother when in use and can maximize functionality and aesthetics in a limited space. Of course, it is not only drawers that have custom slide rails. For example, seats, toolboxes, aerospace, and other application fields also have these needs.
Next, AOLISHENG will tell you what process we will go through and the services you can enjoy when customizing drawer slides (the same applies to slide rails in other application fields).
From design to production: How does our customization process ensure your satisfaction?
In custom drawer slides, every step is crucial, from customer demand analysis to final product production. We are committed to ensuring that every slide rail meets customer expectations through refined management and advanced technology.
Customer demand analysis: Accurately capture your needs
Demand research
Detailed communication: We first communicate with customers in depth to understand their specific needs and expectations. This includes functional requirements, adjustment options, material selection, environmental adaptability, and any special requirements for custom drawer slides. Through face-to-face meetings or online discussions, we ensure that we can fully understand the customer’s needs.
Application scenario analysis: Based on the customer’s application scenario, we analyze their special requirements for drawer runners’ performance. This stage helps us determine the product design’s core direction and technical standards.
Demand confirmation
Technical evaluation: Our engineering team conducts a technical evaluation of the requirements proposed by the customer to determine the technology and materials required to achieve these requirements. This includes considering the strength, durability, adjustment accuracy, and safety standards of the slide rail.
Scheme formulation: Based on the results of the demand analysis, we formulate a preliminary design plan and confirm it with the customer. The plan will include design drawings, a list of materials, and functional descriptions to ensure that the customer’s expectations of the final product are consistent with the actual design.
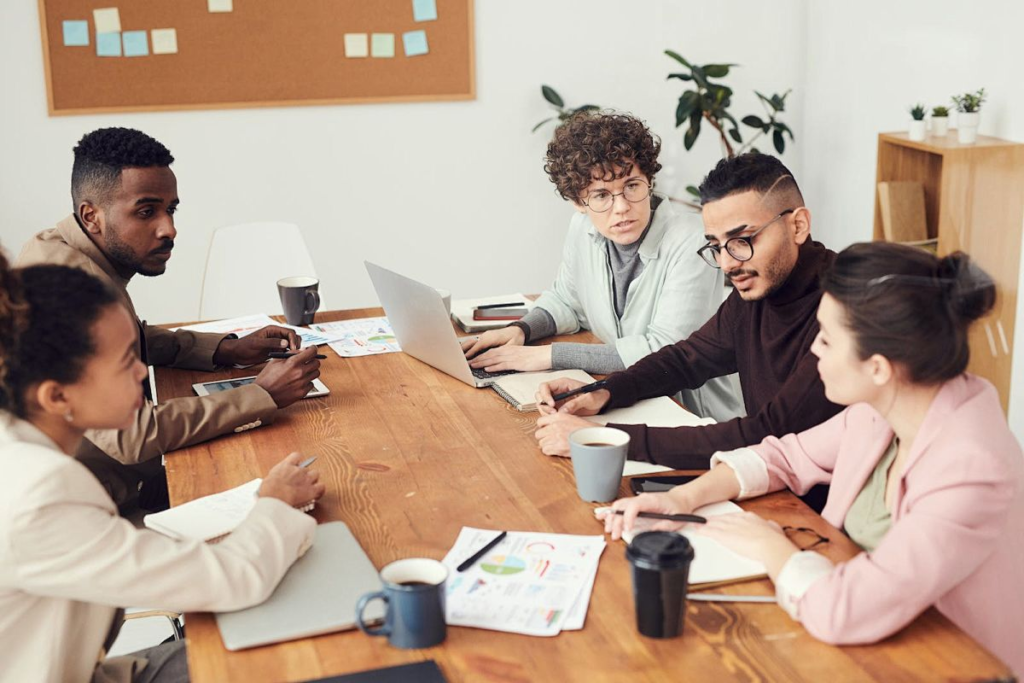
Slide Design: From Concept to Detailed Drawings
Preliminary Design
Conceptual Design: Based on the confirmed requirements, we conduct conceptual design and propose a variety of custom drawer slides solutions for customers to choose from. Each solution will describe the main functions, material selection, and design concept of the drawer runners in detail.
Design Review: After the preliminary custom drawer slides design is completed, we organize a design review meeting to review the design details with the customer to ensure that all requirements are met. Customer feedback will be used to optimize the design solution.
Detailed Design
CAD Modeling: Once the conceptual design is approved, we use computer-aided design (CAD) software to create detailed 3D models. These models will include every component, size, interface, and assembly method of the drawer runners.
Design Verification: During the detailed design stage, we conduct simulation tests and analysis to verify whether the custom drawer slides design can meet the expected performance standards in actual applications. Including durability, stability, and safety tests.
Design Confirmation: After completing the detailed design, we provide the final design drawings and specification documents to the customer for final confirmation. Ensure that every detail meets the customer’s requirements and obtain final approval before entering the mold production stage.

Production process: ensuring quality at every stage
Material procurement
Supply chain management: We purchase high-quality raw materials from trusted suppliers through strict supply chain management. All materials are quality tested. Although the basic raw material Q235 steel selected by AOLISHENG is recyclable, AOLISHENG promises to never use recycled steel for recycling to ensure compliance with design standards and industry specifications.
Material testing: All purchased materials will be tested before production, including strength, wear resistance, corrosion resistance, etc., to ensure their application performance in the slide rails.
Manufacturing
Advanced Equipment: During the production process, we use advanced manufacturing equipment and technology, such as CNC machines, laser cutting, and precision milling, to ensure the accuracy and consistency of each slide rail component.
Process Control: Each step of the production process is subject to strict quality control. We implement standard operating procedures (SOP) and conduct real-time monitoring to ensure that each component and final product meets the design specifications.
Quality Inspection
Functional Testing: After production, all custom drawer slides need to pass functional testing, including raw material hardness, tensile testing, steel ball specification screening, corrosion resistance testing, low-temperature environment testing, and life cycle testing to ensure their reliability in actual use.
Appearance Inspection: We conduct an appearance inspection on each custom drawer slides to ensure that there are no flaws or defects. All products must undergo a series of rigorous inspections before entering the final packaging stage.
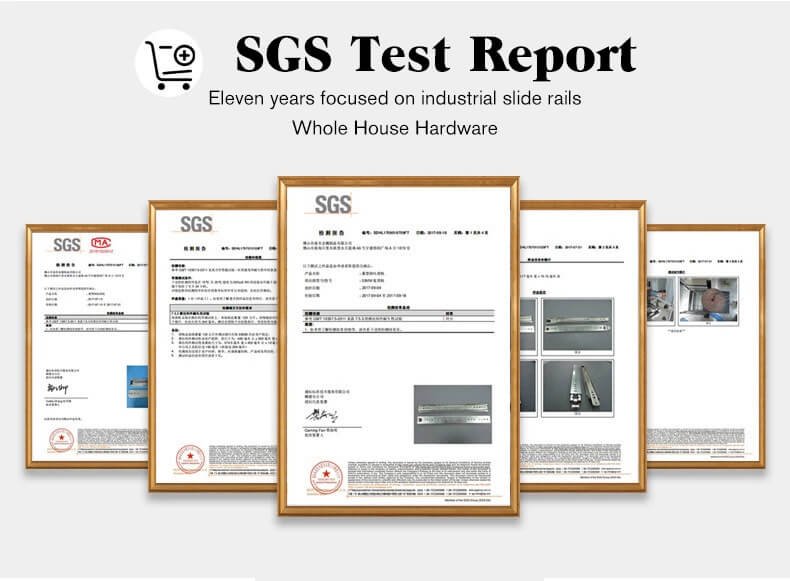
Delivery and Service: Ensuring Your Satisfaction and Support
Product Delivery
Packaging and Transportation: After quality inspection, all slide rails will be packed according to internationally recognized standards to prevent damage during transportation. We work with reliable logistics partners to ensure that the products are delivered safely and on time to the customer’s designated location.
Delivery Confirmation: After the product is delivered, we will confirm with the customer to ensure that the product meets expectations. Any problems encountered during the delivery process will be resolved promptly.

After-sales service
Technical support: We provide comprehensive technical support, including installation guidance, instructions for use, and troubleshooting. Our technical team is always ready to answer any questions from customers and ensure the normal use of the product.
Customer feedback: We value customer feedback and regularly collect customer experience and satisfaction with the product. Customer suggestions will be used to improve product design and service processes to further enhance our product quality and customer satisfaction.
Flexibility of customized services: solutions to meet small and large orders
Whether it is small-batch customization or large-scale production, we are committed to providing flexible and efficient solutions to meet various customization needs.
Small batch customization: accurate and fast personalized service
Challenges of small batch production
Design flexibility: Small batch customization usually involves personalized needs, which require design adjustments according to specific requirements. We provide flexible design services, can quickly respond to customers’ customization requests, and adjust the design scheme to meet specific small batch needs.
Cost control: Small batch production may face high unit costs. We optimize the original drawer runners model and try to modify the slide through the original mold. We try our best to reduce production costs while maintaining high-quality standards. Customized production lines and efficient process management help us achieve cost control and high-cost performance.
Solutions
Rapid prototyping: We provide rapid prototyping services so that customers can verify the design before formal production. This stage helps customers understand the actual effect of the product in advance and avoid design errors and situations that do not meet expectations.
Small batch production: We have a dedicated small batch production line that can complete the production of small orders in a short time. The flexibility and efficiency of the production process ensure the fast delivery and high-quality standards of small batch orders.
Personalized service: In response to the personalized needs of small batch orders, we provide dedicated project managers and technical support to ensure that each order is carefully managed and serviced. Customers can consult and adjust their needs at any time to ensure the conformity of the final product.
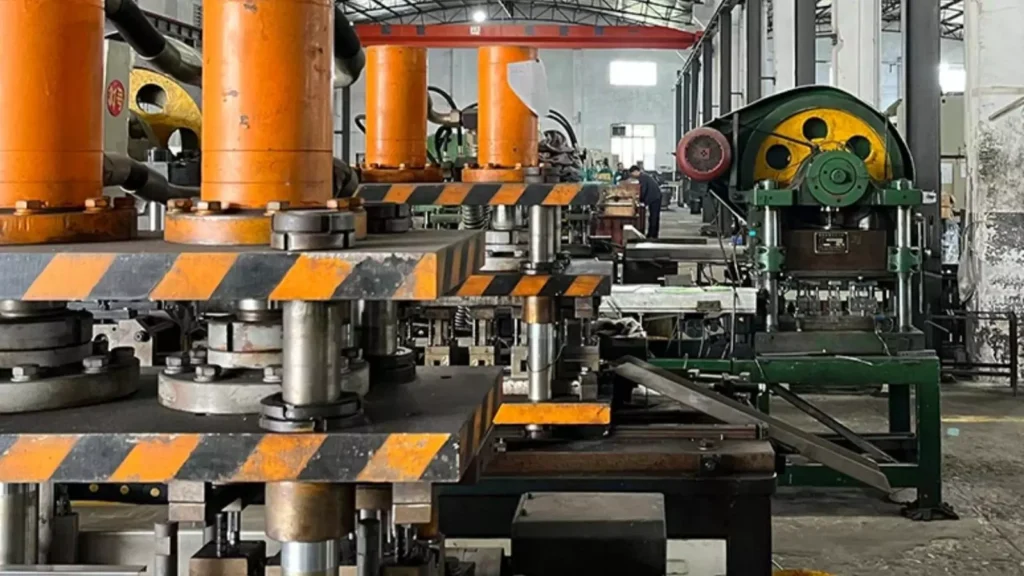
Large-scale orders: efficient and stable production capacity
Challenges of large-scale production
Production efficiency: Large-scale production requires efficient production lines and management systems to ensure production efficiency and delivery time. We use advanced production equipment and automation technology to improve production efficiency while maintaining consistency in product quality.
Supply chain management: Large-scale production involves the procurement and management of a large amount of raw materials. We ensure the stable supply and quality of raw materials by establishing long-term cooperative relationships with suppliers. At the same time, we optimize inventory management and logistics arrangements to reduce production cycles and delivery times.
Solution
Large-scale production line: We have large-scale production lines that can handle the production needs of large orders. The standardized and automated processes of the production line ensure efficient production capacity and stable product quality.
Quality control: Quality control is particularly important in large-scale production. We implement a strict quality management system, from raw material inspection to real-time monitoring during production to final product inspection, to ensure that every product meets the standards.
Flexible scheduling: Our production system has flexible scheduling capabilities and can quickly adjust production plans according to changes in orders. This flexibility allows us to adapt to changing needs in large-scale orders and ensure on-time delivery.

Optimization of customized solutions: Full process management from production to delivery
Pre-production preparation
Demand analysis: Whether it is a small batch or a large-scale order, we conduct a detailed demand analysis to understand the specific requirements of the customer. This includes design requirements, functional requirements, delivery time, etc., to formulate the most appropriate production plan.
Production plan formulation: Based on the results of demand analysis, we formulate a detailed production plan, including production schedule, resource allocation, and quality control measures. The optimization of the production plan ensures production efficiency and product quality.
Management in production
Real-time monitoring: During the production process, we conduct real-time monitoring and management to ensure that production proceeds as planned. Through data collection and analysis, we can promptly identify and solve problems in production to avoid affecting delivery time.
Flexible adjustment: For small batch orders, we provide the ability to quickly adjust to respond to design changes or demand adjustments. For large-scale orders, we ensure the flexibility of the production line and can make necessary adjustments and optimizations in large-scale production.
Delivery and follow-up services
Precise delivery: We optimize logistics and distribution solutions to ensure that products can be delivered to customers on time. Whether it is a small batch or a large order, we provide precise delivery time and tracking services.
After-sales support: Provide comprehensive after-sales support, including product usage guidance, maintenance advice, and technical support. Our service team is always ready to solve any problems encountered by customers during use to ensure customer satisfaction.
Cost-effectiveness analysis: How can custom drawer slides achieve high performance within a budget?
In the process of custom drawer slides, achieving a balance between high performance and cost-effectiveness is the key. Customers want to get high-quality custom drawer slides solutions within their budget, which requires us to manage design, production, and material selection in detail.
Material selection: efficient use of cost and performance
Optimize material selection
Cost-effective materials: We select cost-effective materials to meet different performance requirements. For example, using alloy steel or engineering plastics instead of expensive materials can maintain the strength and durability of the drawer runners while controlling costs. Choose the right material according to the application requirements, such as aluminum alloy, carbon fiber composite material, or stainless steel, to achieve the best balance between performance and cost.
Bulk procurement: Through bulk procurement and long-term partnerships, we can get more favorable material prices. This procurement method reduces the unit price of raw materials, thereby saving on overall production costs.
Material performance and cost comparison
Performance testing: During the material selection stage, we conduct rigorous performance testing to ensure that the selected materials can meet performance requirements without introducing unnecessary costs. Through scientific material performance evaluation, we can find the best balance between cost and performance.

Design optimization: reduce unnecessary expenses
Simplify design
Function and structure optimization: By streamlining the design and optimizing the structure, we can reduce the complexity of the production process and reduce manufacturing costs. For example, reducing unnecessary design elements and complex assembly processes can effectively reduce production difficulty and cost.
Standardized components: Try to use standardized components and modular design to reduce the need for customized parts. Standardized components can reduce production costs and maintenance costs while shortening production cycles.
Production process optimization
Efficient manufacturing process: Use advanced production processes and automated equipment to improve production efficiency and accuracy. Automated production lines reduce labor costs and production time while improving product consistency and quality.
Reducing waste: By optimizing production processes and reducing raw material waste, we can reduce production costs. Implement lean production and continuous improvement measures to ensure efficient operation of each link and rational use of resources.
Production scale and cost-effectiveness: Considerations for small batch and large-scale production
Small batch production
Quick response and flexible adjustment: In small batch production, we provide quick response and flexible adjustment services to meet customers’ personalized needs. Although the unit cost of small batch production is higher, we try to reduce it as much as possible by optimizing the design and production process.
Customization service: Small batch customization allows customers to make design adjustments and functional optimizations according to their needs to ensure that each product meets specific requirements. Although the cost of customization is higher, it can provide high-performance solutions within the budget.
Massive production
Economy of scale: In mass production, we use economies of scale to reduce the production cost of a single product. Through mass production and automated equipment, the unit production cost is reduced while improving production efficiency.
Long-term contract: We can get you a more favorable price for large-scale orders through long-term agreements and bulk purchases. The fixed costs of mass production are spread over each slide rail, further reducing costs.
Performance testing and quality control: ensuring high-cost performance
Strict performance testing
Performance evaluation: Before and during production, we conduct rigorous performance testing to ensure that the custom drawer slides meet the design requirements and can operate stably in actual applications. The results of performance testing are used to optimize design and material selection to ensure that each product has high performance.
Quality control: Implement comprehensive quality control measures, from raw material inspection to production process monitoring to final product testing, to ensure product quality and consistency. High-quality control can reduce failure and rework costs and improve the long-term benefits of products.
Customer feedback
Continuous improvement: Collect customer feedback and make product improvements based on actual usage. By continuously optimizing product design and production processes, we can further improve the cost performance of custom drawer slides and achieve higher performance within budget.
Quality Assurance: How do we ensure the high quality of each custom drawer slides?
In the production process of custom drawer slides, ensuring the high quality of each product is our core commitment. From design to production to final inspection, we implement a series of strict quality control measures to ensure the performance, durability, and reliability of the drawer runners.
Design stage: accurate demand analysis and optimized design
Demand analysis
Customer demand research: Before the design begins, we communicate with customers in depth to understand their specific needs and application scenarios. This includes functional requirements, usage environment, load bearing, etc., to ensure that the design can meet the requirements of actual use.
Technical specification confirmation: According to customer needs, we formulate detailed technical specifications and design parameters. This includes the size, load capacity, adjustment range, etc. of the custom drawer slides to ensure that the design meets the expected performance standards.

Design optimization
Simulation and simulation: During the design process, we use advanced computer-aided design (CAD) software and simulation tools to simulate the performance of custom drawer slides. This helps us identify potential problems and optimize the design before actual production to ensure the reliability and stability of the product.
Design review: Each design solution undergoes multiple rounds of review and verification, and a professional team of engineers checks the feasibility and rationality of the design to ensure that all design details meet standards and customer requirements.
Material selection: ensuring the quality and performance of materials
Material selection
Quality suppliers: We work with certified material suppliers to ensure that the materials used meet international standards. The selection of materials includes Q235 steel, stainless steel, aluminum alloy, etc., which are selected according to the specific needs of the slide rail.
Material inspection: All materials undergo strict quality inspection before being put into production, including physical property testing, chemical composition analysis, and corrosion resistance testing. Only materials that meet quality standards can enter the production line.
Material testing
Performance verification: For key materials, we conduct special performance tests, such as corrosion resistance testing, wear resistance testing, etc., to verify their performance in actual use. These tests ensure the long-term durability and stability of the materials.
Batch tracking: Each batch of materials is tracked and managed, and the entire process from procurement to use is recorded to ensure that the source of the materials can be traced and facilitate rapid processing when problems are found.
Production stage: strict process control and management
Production process
Standardized production: We use standardized production processes and procedures to ensure that the production process of each custom drawer slides meets consistent quality requirements. Automated equipment and precision processes improve the accuracy and consistency of production.
Process optimization: During the production process, we continuously optimize the process to reduce errors and defective products in production. Improve production efficiency and product quality by improving production processes and technologies.
Production monitoring
Real-time monitoring: During the production process, we track the production of each slide rail through a real-time monitoring system, including equipment status, production speed, and process parameters. Instantly discover and solve problems in production to ensure stable product quality.
Process review: Regularly conduct production process reviews to evaluate potential risks and problems in the production process and take preventive measures to ensure production continuity and high product quality.
Inspection and testing: comprehensive quality inspection
Initial and intermediate inspection
Initial inspection: Each production batch of custom cabinet drawer slides undergoes preliminary inspection before leaving the factory, including dimensional measurement, appearance inspection, and functional testing to ensure that they meet the design specifications and standards.
Intermediate inspection: During the production process, we conduct intermediate inspections to check the quality of key process steps and intermediate products to ensure consistency and stability in the production process.
Final inspection
Comprehensive testing: Each custom cabinet drawer slides undergoes a final inspection after production. This includes load testing, durability testing, smoothness testing, etc. to verify whether its performance meets the design requirements.
After-sales service and feedback: continuous improvement and customer support
After-sales service
Technical support: We provide comprehensive technical support and after-sales service to help customers solve problems encountered during use. Customers can get timely help and solutions through our service channels.
Product maintenance: Provide detailed product maintenance guidance to help customers keep the custom cabinet drawer slides in the best condition and extend their service life. We will also follow up on product usage regularly to ensure customer satisfaction.

Customer feedback
Collect feedback: Regularly collect customer feedback to understand their product experience and improvement suggestions. This feedback helps us continuously improve product design and production processes, and enhance product quality and performance.
Continuous improvement: Based on customer feedback and market demand, we continuously optimize products and services to ensure that our custom drawer slides always meet the latest quality standards and customer expectations.